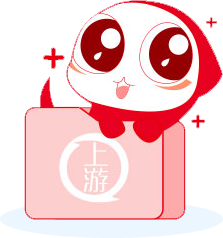

走进北京现代工厂,感受品质匠心
4月24日下午,2018年北京车展前夕,记者造访了位于北京顺义的第二工厂。这是北京车展期间,北京现代借地利优势组织的一次特殊的工厂开放活动。活动中,来自全国各地的媒体不仅参观了以“5个100%”为代表的自动化生产线、王志伟创新工作室,还听取了来自北京现代关于质量管控和新能源汽车发展方面的有关介绍。
领先全球 以智造驱动企业高质量运行
和其他汽车企业一样,北京现代的工厂由冲压、车身、涂装、总装以及发动机工厂组成。但在北京现代车间里,最直观的感受就是大量机器人和省力化设备应用,尤其是在冲压、车身车间,机器人的数量已经多于现场工作人员的数量,“5个100%自动化”是北京现代自动化水平的最直观体现。
目前,北京现代仁和二厂采用全球领先的设备和自动化工艺,其中,冲压车间采用5400吨全自动模块冲压生产线,金属板件生产自动化率达到100%;车身车间全部采用智能焊机,拥有300套机器人,实现焊接自动化率100%; 涂装车间应用环保工艺及先进设备,中、上涂内外板喷涂自动化率100%;总装车间采用多车型混线生产体系,实现车型互换交叉生产100%,发动机车间采用多机型混线生产体系,机加工艺自动化率100%。
在总装车间参观时,大量省力化设备的广泛应用给记者留下了深刻的印象。在北京现代总装车间装配过程中,凡是重量超过三公斤的单件物品,如玻璃、座椅、备胎等配件,全部由机器人或省力化设备帮助人工辅助安装,最大程度减轻工人的工作强度,提高生产效率,避免因劳动负荷过大而产生质量瑕疵,保障整车在细节上的高品质。
严守品质 建设行业一流质量运营体系
北京现代将品质经营的理念全面贯彻到设计、采购、生产、销售、售后等各个环节,打造了一流的质量运营管理体系,严守每一个环节的质量管控。
在工厂参观结束后,质量保证部的质量工程师向记者详细介绍了北京现代质量运营体系。
据介绍,为了保证质量,在专业化队伍建设方面,北京现代质量运营室专门设置8部32个职能科室进行质量控制,管理范围覆盖新车开发质量确保、量产工厂质量管理、动力总成质量管理、售后质量管理及体系、部品实验、计量管理等质量保证过程。
供应商零配件管理,是质量管控的第一个环节。北京现代还对外协企业采用4M方式进行管理,实时审批供应商在生产过程中可能对重要配件质量产生影响的工人、机器设备、原材料、生产方法四个环节,任何改变都要通报北京现代经过确认后才能进行。此外,北京现代还在整个配套体系中长期贯彻“两个评价”,即每年委托第三方对所有配套企业进行5星评价及SQ-MARK评价。以竞争机制对配套企业实现优胜劣汰,保障供应链健康稳定。
北京现代通过专业化队伍建设、上游质量及供应商管理、生产过程管理以及质量检测,构建起一套行业领先的质量运营体系,以国际一流标准及管理全力呵护产品的国际一流品质,为企业持续快速的高质量发展添砖加瓦。
传承匠心 用工匠精神推动品质及效率跃升
成立至今,北京现代始终认为匠心才是保证其品质运营的根本。在生产制造过程中,每一个车间、每一个个体都在传承北京现代的“工匠精神”。
冲压是汽车制造的第一步,“车辆的品质,不能输在起跑线上”。因此,多年来,北京现代冲压一线的师傅们一直坚守一个标准:竭尽全力保证每一个冲压件完美无暇。冲压车间技术人员张涛练就一项不平凡的能力———“电子眼”。一次在调试前门内板时,他看到第一序的模具安装方向有偏差,而在场的其他技术人员都觉得没问题。但在北京现代的生产车间里,只要在质量把控上有疑问就会实行一票否决,整条生产线停线查找问题并解决。为了验证模具安装方式是否正确,大家将制件与制件原型样本各项参数进行逐一比对,最终,微小的数据差异证明了张涛“电子眼”的神奇。
优异的产品品质是北京现代高速前进的基石,而比肩世界顶级工厂的智能化的生产制造技术、领先行业的质量运营体系、融化在全体员工血液中的工匠精神则是构成这块基石的基本元素。 十六年来,北京现代通过对产品品质的坚守和传承赢得了九百三十万客户的认可,推动了企业的高质量发展。